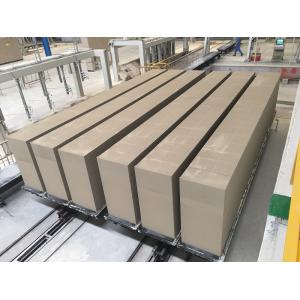
Add to Cart
High Profit Low Invest Small aac Brick Block Production Line
Basic Introduction:
Autoclaved Aerated Concrete (AAC) is a siliceous material (sand, fly ash and silicon tailings such as waste porcelain clay, stone processing waste materials, blast furnace slag, etc.) and calcareous materials (lime, cement) as the main raw material, mixing fat gas agent (aluminum powder), by ingredients, mixing, casting, pre-raising, cutting, autoclave, curing process made of light porous silicate products, because by the hair contains a lot of gas even after the small pores, hence the name of aerated concrete.
Advantage of AAC:
Main Equipments in AAC Production Line:
Material-milling Equipments:
a. Crusher: Lime, gypsum, and such kind of bulk material need to be crushed as the first step in AAC Plant.
b. Miller: The AAC material must be fully grinded in order to make better reaction. Ball Mill is used widely, it has two types: dry and wet, can be chosen upon requirement.
Material Metering Equipments: Computer Control Automatic Metering System is commonly used as measurement of raw materials.
Material mixing and casting equipments: Mixer, it’s the slurry mixing machine, also is slurry casting machine.
Cutting Machine: the AAC blank is formed after casting and pre-curing, as the size is too large, it must be cut to achieve the required product size.
Autoclave: Autoclave is a device for silicate hydration products to get physical and mechanical properties.
Boiler: the boiler supports for the autoclave and pre-heat furnace and other facilities with heat.
Auxiliary Equipments:
a. Mould Frame, Mould Bottom and Mould Car, they composed together to form the Casting Mould, which is the main forming equipments in AAC Production Line.
b. Hardening Car, Ferry Cart and Hangers, they must be equipped as auxiliary equipments in autoclave curing system.
c. Block Separator. The separator is a special machine whose function is to separator the plaste block into piece,in order to be transfered and used.
d. Block packing machine.
The process flows of the plant line
Dose the raw materials(1), then convey the raw materials to the casting and mixing machine, mix them(2), evenly cast them(3) put the reinforcing bars in the mould(19). After a period of static curring(4), once the green brick gains certain degreen if hardness, it will be conveyed to the cutting machine together with the mould. The turning over sling complete the following works:A, turning over the mould with 90 degrees in the air(5), one side boards becomes the base board to support the green brick intil it is steam cured. B, swing the green brick to the cutting cart or cutting board to demould(6). C the unload mould frame and the returning side board(16)are recombined into mould again. (17) the recombined mould will be cleaned and sprayed with oil for casting again. (18) Each face of the green brick will be cut on the cutting machine step by step: a, cutting the sides of the green brick vertically(7), b, then cutting it crossly(8), at last, cutting the green brick horizontally(9). After cutting, the green brick together with mould base plate are swinged to the steam curing cart(10) and numbered before sending into the autoclave(11) for high temerature steaming curing(12), after steam curing, the bricks are taken out of the autoclave(13), and then swinged to pile up or load it to a car and packaged(15), the side board is sent back to the beginning of the production line(16).