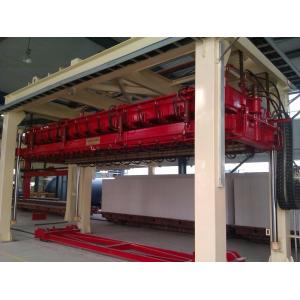
Add to Cart
AAC Block Production Line, AAC Block Machine, AAC Blocks Price
Raw material proportion of AAC Block Machine :
A--Cement lime fly ash style aerated block raw material proportion
Name | Unit | Cement lime fly ash |
flyash | % | 65-70 |
cement | % | 6-15 |
lime | % | 18-25 |
gypsum | % | 3-5 |
Aluminum powder paste(600kg/m3) | 1/10000 | 8 |
Water & material rate | 0.60-0.65 | |
Casting system | OC | 36-40 |
Aluminum mixing time | S | 30-40 |
B-- Cement lime Sand style aerated block raw material proportion
Name | Unit | Cement Lime Sand |
Sand | % | 55-65 |
Cement | % | 10-20 |
Lime | % | 20-30 |
Gypsum | % | 2-3 |
Aluminum powder paste(600kg/m3) | 1/10000 | 8 |
Water & material rate | 0.65-0.75 | |
Casting system | OC | 35-38 |
Aluminum mixing time | S | 30-40 |
Detailed information of of AAC Block Machine :
Foam block machine, aerated autoclaved concrete plant, dong fang AAC block,dongfang aac production line,dongfang aac plant,AAC brick,autoclave aerated concrete block,concrete block machine,light weight block.
1) Product weight is according to 600kg/m3 to control.
2) Annual capacity 200,000M3.
3) Set raw material proportion: cement 6.5%, raw lime 23%, flyash 68%, gypsum 3%, aluminum paste powder 350g/M3.
4) Water and material rate 0.631
5) One mould product 2.88M3
6) Casting slurry cycle time 5-6 minutes, cut cycle time 5 minutes.
7) Casting slurry temperature 38-42 degree
8) Body quiet stop. Time is 1.5-2.5housr, temperature 50-90 degree, after quiet stop body strength is 0.15-0.18Mpa
9) Steam curing cycle time, come in and out autoclave about 0.5hour, steam curing cycle time about is 6 hours/1.6Mpa, total 6.5 hours
Complete equipments for AAC Block Machine :
1) all kinds of raw materials storage bin→ (2) measuring and batching → (3) mixing raw material with water → (4) prepared mould (5) → pouring → (6) vesicant and static curing → (7) demoulding → ( 8) rolling-over: horizontal cutting, vertical cutting → (9) be grouped into the autoclaved kettle → (10) high temperature and high pressure conservation → (11) out of autoclaved kettle for finished product → (12) testing finished product → (13)packaging → (14) stacking storage → (15) out of factory
Below is pictures of our clients: